Building a DIY Surgical Robot: An Innovation in Medical Technology
Have you ever watched a robotic-assisted surgery and thought, “I wish I could operate a machine like that?” Well, now you can, thanks to DIY enthusiasts who have taken on the challenge of building their own surgical robots. Inspired by the expensive costs of purchasing and maintaining professional surgical robots, these individuals have taken matters into their own hands to create their own versions using used medical instruments.
The journey begins with acquiring a surgical instrument, like a Suture cut needle driver, from a used medical device vendor on eBay. These instruments, designed for compatibility with professional surgical robots, provide a starting point for understanding the mechanical relationships necessary for creating a DIY robot. Through trial and error, these enthusiasts navigate the complexities of the instrument’s movements and translate them into code for electronic control.
While the process is challenging and requires a deep understanding of mechanics and electronics, the possibility of creating a functional surgical robot from used instruments is an exciting prospect. With determination and ingenuity, these individuals are paving the way for a new era of accessible medical technology.
Watch the video by Bennett Stirton
Video Transcript
You’ve seen this video or at least you have now this is footage of a robotic assisted surgery granted this is being done on a grape but I hope that this is as cool to you as it is to me I don’t know exactly when I saw this video but
As soon as I learned about this technology I was positively enamored I really wanted to operate a machine like this barring 8 to 12 years of medical school and surgical residency the only other way I think I’d be able to operate one of these machines would be to buy
One outright let’s see how much one of these bad boys costs $2 million and that’s not all annual maintenance is something to the tune of $175,000 and there are additional expenses incurred every time the robot is used these are for consumables things like covers PPE for the Rob robot and
Its favorite snacks consumables so I eventually accepted that the only way I’d get to see one of these medical Marvels in person would likely be under anesthesia if you catch my drift but times have changed I recently learned a bit more about the da Vinci Suite of surgical
Tools and solutions offered by intuitive surgical you see the robot stays put that’s a heavy boy it’s not going anywhere in addition to the robot intuitive surgical cells instruments which are basically the accessories that attach to the robot robot and allow the robot to perform any number of incredibly complex surgeries these
Instruments are of course sterilized between uses and some of these instruments especially the more mechanically complex ones are going to experience some accelerated wear and tear due to the sterilization cycle perhaps because of this intuitive gives each surgical instrument a lifespan a number of uses that the instrument is
Good for before it needs to be replaced some may say this 10 to 15 punch limit is a safety feature to make sure that a mechanical failure never occur occurs in the middle of surgery some may also say that limiting the instruments to 10 uses is just an example of planned
Obsolescence forcing these hospitals to Pony up and pay for more instruments to use the surgical equipment that they already purchased whether it’s about safety or money the outcome is all the same every year thousands of these surgical instruments mostly in perfectly good working order need to be disposed
Of some hospitals throw these used instruments into their trash shoot but some hospitals sell them on eBay me to get started I purchased one instrument from a used medical device vendor on eBay this was for me to figure out if reanimating one of these things would even be possible this is the large
Suture cut needle driver and served as my sort of entryway into this world this is the perfect surgical instrument to start out with because it features intuitive surgicals and Endor wrist technology which is basically their patented mechanism or maybe series of mechanisms that explain exactly how they
Are able to create wristed motion in such a small space this carbon fiber shaft is only 8 mm wide it’s very lightweight and the entire system is cable driven now I have yet to take one of these apart myself but if this is something you’d be interested in seeing
Please drop a like or a comment after I received my first instrument it was time for me to figure out if reanimating one of these things would even be possible now in a world of proprietary connections and uh decreasing rights to repair I was fully expecting this thing
To be pretty much inoperable without the rest of the machine but thankfully because of the almost entirely mechanical nature of this instrument which again in part is necessary because these things are sterilized there’s nothing to really stop someone like you or I from acquiring one of these
Instruments new or used and using it for our own purposes so I set up some eBay alerts to figure out if I could purchase maybe a lot of these instruments they’re not particularly expensive but you could probably buy about 10 gallons of almond milk with the money I’d spend on one of
These so I definitely wanted to try to get bulk pricing if possible and I ended up just barely winning an auction for two single sight sets the goal of these sets is to include everything a surgical team might need in the operating room to perform a robotic assisted single sight
Surgery this includes a number of different instruments as well as all kinds of different tro cars and mounting apparatuses these single sight sets included two different types of instruments these green ones which have sort of a floppy thinner shaft and only have two degrees of freedom
And these blue ones as you see here these have a rigid 8 mm carbon fiber shaft in part to accommodate the increased mechanical complexity inside we’ll save the green ones for later okay great I’ve got all the instruments I could ever need So the plan then is to figure out exactly how
This thing works make a model of any necessary mechanical relationships and based on that I should be able to make the electronics from there it’s as simple as building the rest of the robot and making everything talk together and before you know it we should be taking
Care of some produce patients we know that there are four inputs to the instrument here four corresponding discs to control those inputs and four Motors to spin the four discs now the da Vinci SI robot that these instruments are compatible with has four robotic arms three of them you’ll put an instrument
On and one of them is for the endoscope because these instruments are sterilized between each use it makes sense to have the electronics the uh Motors and basically anything of value inside the robot arm itself so I threw together a super rough prototype which has four Motors and some discs to allow this
Thing to couple with the instrument typed up some code and immediately broke my prototype what happened you asked I have the same question turns out the cable driven nature of these instruments results in what you might call coupled motion even though there are four different inputs none of these inputs
Operates truly independently of the others with the except of the rotation of the device every other disc is in some way coupled with the other discs it’s critical then to understand how each disc’s movement relates to the other movements and how the limits of each disk change as a function of the
Other disc’s movements otherwise if I try to flex the instrument around its abduction axis uh I might accidentally clamp down on something I don’t mean to clamp on so I did some good old trial and error to figure out these relationships in order to then translate these relationships into code this
Started by labeling each of the discs to help keep track of things there is some sort of neutral point for both the disc and the pulley that it controls inside of the actual instrument so for the rest of the testing I placed everything at that 12:00 position to try to isolate
Variables from there it was as simple as identifying the different axes of movements and then manipulating the end affector to see what affected what and I summarized my findings here basically if you wish to have a 90° abduction in either direction you would need to see these rotations of the disc assuming
That you don’t want anything else to move you can see that this is also true for whatever kind of jaw the instrument is equipped with whether it be scissors or clamping anything like that for the Jaws to go from the closed state to the open State it’s as simple as ensuring
That the Delta between disk B and C increases by 30° clockwise this could be achieved by increasing the rotation of dis B by 30° by decreasing the rotation of dis C by 30° or as you’re probably thinking yes anything in between Plus 15b minus 15 c will get you the same outcome as
Well now with this understood I can make a semi-reliable semi- functioning prototype that will allow me to figure out the rest of my design I also learned that I needed to upgrade these small 9 G Servo Motors to something a bit bigger and more up to the challenge these
Larger servos have more torque and also feature metal gears on the inside which should hopefully decrease the amount of damage that I incur now while I thought these servos would be perfect I immediately encountered another issue although they can fit side by side these servos are literally 1.5
Mm too long to be stacked end to end my options were either to make some kind of gearbox or basically stadium seating instead that way everybody can be coupled directly with their axis uh which is great because fewer parts for me to mess up and fewer things to go
Wrong I’d emphasize the motors because I watched a number of different Da Vinci training videos some some authorized and some not and I could never quite get an understanding of how exactly these instruments attached to the machine you see all of the reference videos I collected show the instrument sliding
Into place but the discs which are how the instrument actually connects to the motor all have these locating pins here I’m not sure exactly how this instrument can be attached in One Direction when the motors need to connect in another so I had to figure out my own solution this
Is far from final but for the sake of a functioning prototype I made a spring-loaded four bar mechanism this allows the motor pack as I’m calling it to drop down and disengage from the docked instrument after which the instrument can slide out and be replaced with a different one thankfully
Designing this mechanism was a walk in the park that’s a lie I had to learn a new CAD program for this and once I 3D printed it I learned that my design was perfect and it worked on the first try these failed prototypes would beg to differ
This leads me to one of my favorite features of this design which is this springy thing this is a 3D printed orthop planer spring Ortho meaning the direction of deflection and rotation are at right angles to one another and spring meaning it goes like this now I
Can’t take credit for this super cool spring the design is by the amazing Folks at the BYU compliant mechanisms research group and I will link to both their file and website below this is helpful for my application because it allows these connecting displate things to comply and flex up
And down while the motors find their Mark in a homing sequence but they still effectively transfer rotation between the motor and the instrument now the end goal is obviously to have this on a robotic arm but I need to focus on one thing at a time so I
Repurposed this old monitor arm from Facebook Marketplace this monitor arm is just like any one you’d find on Amazon and features the standard standard vesa mounting plate I just ripped that off so I could bolt directly onto the arm and it ended up working pretty well for my
Application except for the fact that these gas Springs that allow the monitor arm to move up and down have a maximum load but also a minimum load and in my efforts to keep things relatively lightweight my motor pack assembly isn’t heavy enough to make things work so I
Employed an additional weight to uh help things move more smoothly in the meantime this is perfect since it allows me to position the instrument wherever it needs to be in order for me to be able to test things as far as next steps go perhaps even more important than the
Robotic arm is figuring out what input solution I’m going to go with to control my prototype I used a joystick and a simple potentiometer but any good surgical robot is going to have at least two of these instruments not to mention the Litany of motors and
Axis to be accounted for when it comes to actually moving these instruments around so I’m going to need to figure out some kind of intuitive control system pun intended to control upwards of 12 different Motors here’s some footage of surgery being performed with the da Vinci SI and I need to figure out
How to accomplish this without trying to reverse engineer one of these things all I know for now is it probably shouldn’t be voice controlled but I haven’t figured out much beyond that if anybody has any ideas please let me know in the comments now I don’t think this is quite
Ready for a grape appendectomy but I think it’s a good first step if you would like to support me in this ridiculous Pursuit you can do so by hitting the Subscribe button and you can hit the Bell as well if you would like to be notified when the next video drops
Video “Building a DIY Surgical Robot” was uploaded on 02/25/2024 to Youtube Channel Bennett Stirton
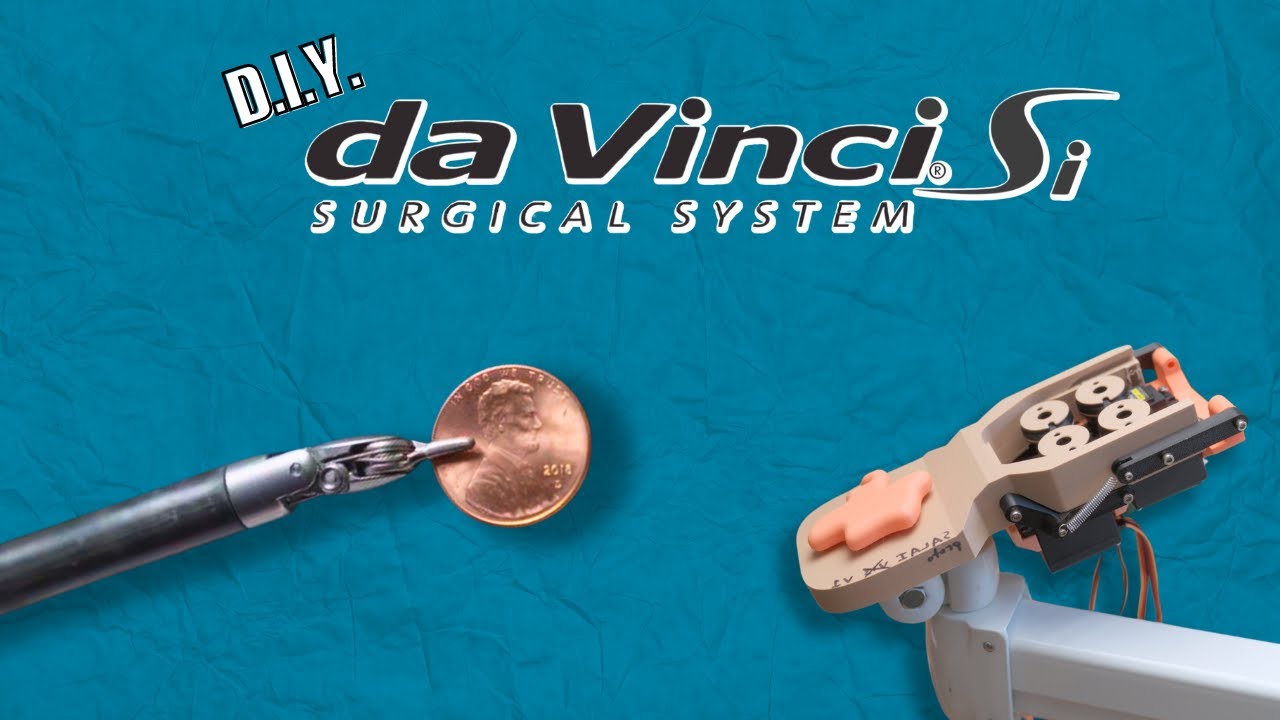
The post “Constructing a Do-It-Yourself Surgical Robot – Video ” by GretAi was published on 02/29/2024 by news.gretai.com