When the computer or phone you’re using right now blinks its last blink and you drop it off for recycling, do you know what happens?
At the recycling center, powerful magnets will pull out steel. Spinning drums will toss aluminum into bins. Copper wires will get neatly bundled up for resale. But as the conveyor belt keeps rolling, tiny specks of valuable, lesser-known materials such as gallium, indium and tantalum will be left behind.
Those tiny specks are critical materials. They’re essential for building new technology, and they’re in short supply in the U.S. They could be reused, but there’s a problem: Current recycling methods make recovering critical minerals from e-waste too costly or hazardous, so many recyclers simply skip them.
Sadly, most of these hard-to-recycle materials end up buried in landfills or get mixed into products like cement. But it doesn’t have to be this way. New technology is starting to make a difference.
Ansan Pokharel/West Virginia University, CC BY
As demand for these critical materials keeps growing, discarded electronics can become valuable resources. My colleagues and I at West Virginia University are developing a new technology to change how we recycle. Instead of using toxic chemicals, our approach uses electricity, making it safer, cleaner and more affordable to recover critical materials from electronics.
How much e-waste are we talking about?
Americans generated about 2.7 million tons of electronic waste in 2018, according to the latest federal data. Including uncounted electronics, a survey by the United Nations suggests that the U.S. recycles only about 15% of its total e-waste.
Even worse, nearly half the electronics that people in Northern America sent to recycling centers end up shipped overseas. They often land in scrapyards, where workers may use dangerous methods like burning or leaching using harsh chemicals to pull out valuable metals. These practices can harm both the environment and workers’ health. That’s why the Environmental Protection Agency restricts these methods in the U.S.
The tiny specks matter
Critical minerals are in most of the technology around you. Every phone screen has a super-thin layer of a material called indium tin oxide. LEDs glow because of a metal called gallium. Tantalum stores energy in tiny electronic parts called capacitors.
All of these materials are flagged as “high risk” on the U.S. Department of Energy’s critical materials list. That means the U.S. relies heavily on these materials for important technologies, but their supply could be easily disrupted by conflicts, trade disputes or shortages.
Right now, just a few countries, including China, control most of the mining, processing and recovery of these materials, making the U.S. vulnerable if those countries decide to limit exports or raise prices.
These materials aren’t cheap, either. For example, the U.S. Geological Survey reports that gallium was priced between US$220 to $500 per kilogram in 2024. That’s 50 times more expensive than common metals like copper, at $9.48 per kilogram in 2024.
Revolutionizing recycling with microwaves
At West Virginia University’s Department of Mechanical, Materials and Aerospace Engineering, I and materials scientist Edward Sabolsky asked a simple question: Could we find a way to heat only specific parts of electronic waste to recover these valuable materials?
If we could focus the heat on just the tiny specks of critical minerals, we might be able to recycle them easily and efficiently.
The solution we found: microwaves.
This equipment isn’t very different from the microwave ovens you use to heat food at home, just bigger and more powerful. The basic science is the same – electromagnetic waves cause electrons to oscillate, creating heat.
In our approach, though, we’re not heating water molecules like you do when cooking. Instead, we heat carbon, the black residue that collects around a candle flame or car tailpipe. Carbon heats up much faster in a microwave than water does. But don’t try this at home; your kitchen microwave wasn’t designed for such high temperatures.
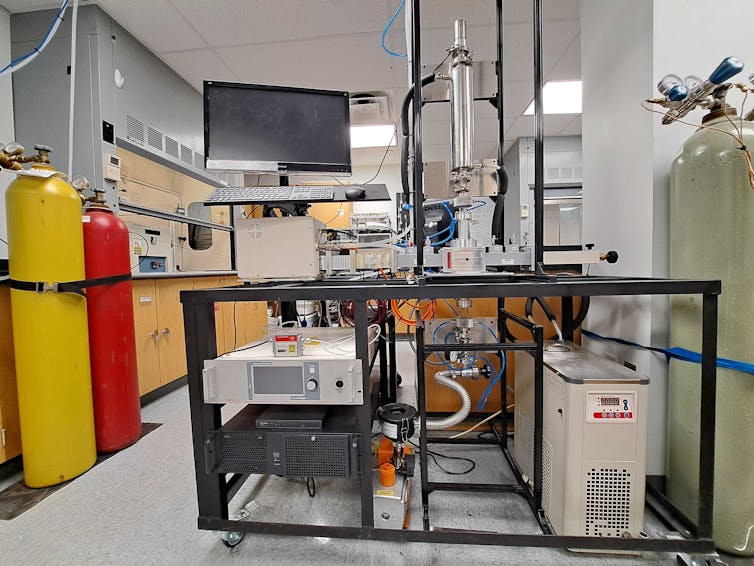
Ansan Pokharel/West Virginia University, CC BY
In our recycling method, we first shred the electronic waste, mix it with materials called fluxes that trap impurities, and then heat the mixture with microwaves. The microwaves rapidly heat the carbon that comes from the plastics and adhesives in the e-waste. This causes the carbon to react with the tiny specks of critical materials. The result: a tiny piece of pure, sponge-like metal about the size of a grain of rice.
This metal can then be easily separated from leftover waste using filters.
So far, in our laboratory tests, we have successfully recovered about 80% of the gallium, indium and tantalum from e-waste, at purities between 95% and 97%. We have also demonstrated how it can be integrated with existing recycling processes.
Why the Department of Defense is interested
Our recycling technology got its start with help from a program funded by the Defense Department’s Advanced Research Projects Agency, or DARPA.
Many important technologies, from radar systems to nuclear reactors, depend on these special materials. While the Department of Defense uses less of them than the commercial market, they are a national security concern.
We’re planning to launch larger pilot projects next to test the method on smartphone circuit boards, LED lighting parts and server cards from data centers. These tests will help us fine-tune the design for a bigger system that can recycle tons of e-waste per hour instead of just a few pounds. That could mean producing up to 50 pounds of these critical minerals per hour from every ton of e-waste processed.
If the technology works as expected, we believe this approach could help meet the nation’s demand for critical materials.
How to make e-waste recycling common
One way e-waste recycling could become more common is if Congress held electronics companies responsible for recycling their products and recovering the critical materials inside. Closing loopholes that allow companies to ship e-waste overseas, instead of processing it safely in the U.S., could also help build a reserve of recovered critical minerals.
But the biggest change may come from simple economics. Once technology becomes available to recover these tiny but valuable specks of critical materials quickly and affordably, the U.S. can transform domestic recycling and take a big step toward solving its shortage of critical materials.
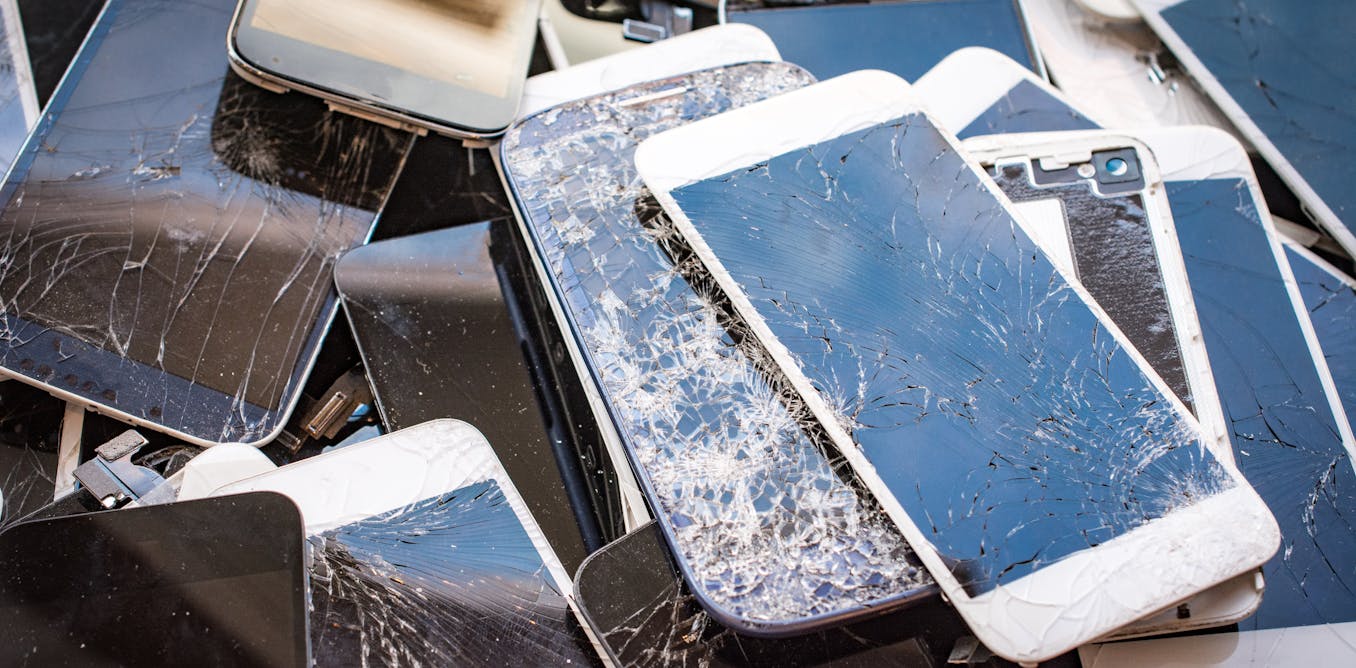
The post “Critical minerals don’t belong in landfills – microwave tech offers a cleaner way to reclaim them from e-waste” by Terence Musho, Associate Professor of Engineering, West Virginia University was published on 05/28/2025 by theconversation.com
Leave a Reply